The DUVRI
What is DUVRI and how it should be written?
The DUVRI means Single Interferential Risk Assessment Document and it is the document that identifies and evaluates risks in the workplace during a contract. It aims to eliminate or minimize interference that may arise from the activities of the companies involved and is regulated by art. 26 of Legislative Decree 81/08.
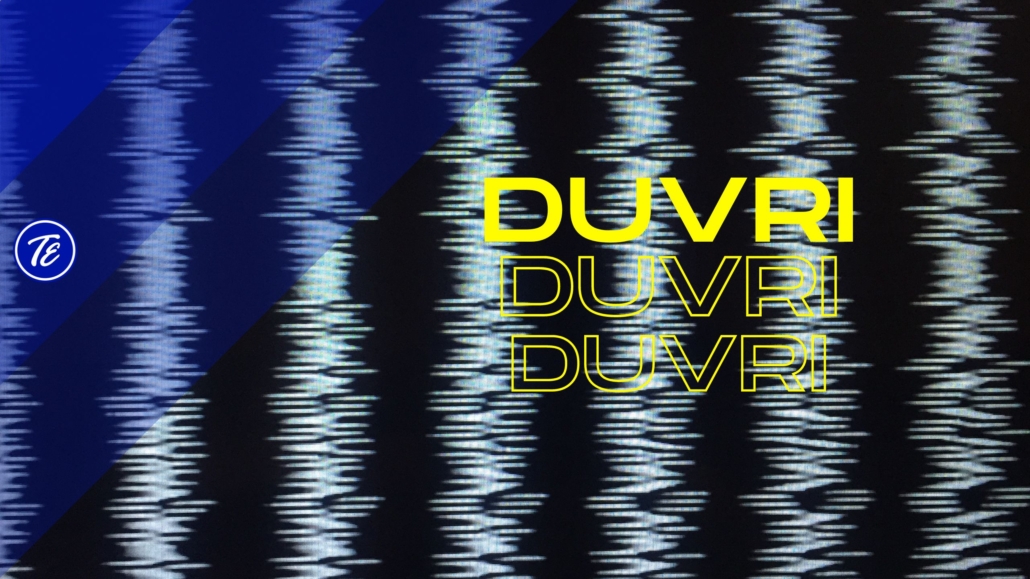
The responsibility for drafting the DUVRI lies with the principal employer for contract works and not with the undertakings or self-employed workers to whom the contract has been awarded. However, they are still required to cooperate and provide all the documents necessary to highlight possible risks. The DUVRI must be prepared or updated each time new contracts are concluded.
The DUVRI is not necessary for the yards where the PSC or Plan of Safety and Coordination has already been prepared and accepted by the executing Enterprises. In these cases, the contractors must prepare the Operational Safety Plan (POS) as the risks of interference have already been addressed by the PSC. The DUVRI must be set up only in situations where it is possible to eliminate or reduce the risk of interference between the contractor’s workers and those of the contractors. If this is not possible, the DUVRI will consist of a statement of the DLC formalizing the impossibility of eliminating or reducing these risks, together with specific justifications of the case. In these cases, the decisions taken during the coordination meeting between all the employers involved, primarily the Employer, will be crucial to ensure safety. It is important to note that the DUVRI is an obligation of the employer, but its drafting can be delegated to third parties.
When it is to be drawn up
According to art. 26 of Legislative Decree 81/08 you have the obligation to draw up the DUVRI when the Employer of a client company entrusts the performance of work or services within its workplace to a contractor or self-employed. But it cannot be drafted for:
- Intellectual nature services,
- supply of materials,
- work or services of less than 5 man-days duration,
- if there is the Security Plan under Coordination.
Art. 29 also informs of obligations:
- information: it concerns the obligation to inform the contractor about the characteristics of the context in which it will operate,
- coordination: it refers to those actions that the employer of the client company must take
- to prevent disagreements, overlaps and other occurrences that may affect safety,
- cooperation: it means that both the employer and the employer must contribute to the preparation and implementation of the necessary preventive and protective measures
The interference risks
Interference risks are classified as risks placed in the contractor’s workplace by the contractor’s work (incoming risks) and as specific risks present in the contractor’s normal business, not normally present in the contractor’s business (risks on exit).
Risks from physical contiguity and space are those risks that arise from overlaps of multiple activities carried out by
several contractors, while the commission risks arise from particular implementing rules, requested by the client.
The DUVRI characteristics
The DUVRI must be integrated with the DVR, even if it is independent of it; it must be finalized to manage the interferential risks and to be single for all the contracts that involve interfering risks.
As regards the minimum content:
- the criteria used must be identified,
- there must be a description of the contracting company and the activities that take place during the contract,
- the activities of the contractors and the working areas available to them shall be described.
Also there must be:
- the chronoprogramme of activities,
- the organisation of the preventive and protective measures to be taken,
- the estimated costs of safety,
- the coordination of work phases.
Update of the DUVRI
When an update of the DUVRI is required, the contracting employer must convene a coordination meeting with the operators involved to identify improvement measures. Some contracts can be affected and adjusted by redefining security costs, or a new contract may be required.